深圳市宏力捷电子有限公司专业提供整体PCBA电子制造服务,包含上游电子元器件采购到PCB生产加工、SMT贴片、DIP插件、PCBA测试、成品组装等一站式服务。接下来为大家介绍SMT贴片加工流程中有哪些制程与注意事项。
不得不说,SMT应该是现代电子组装工业中自动化程度最高的一环,一整条产线大概只需要5-7个作业员就可以维持一条生产线的运作,而且大约每30~60秒就可以产出一片PCBA组装板。
1. 印刷生产序号(Shop Floor tracking number)
SMT产线的前置作业必须要在裸版(bare PCB)上先印上生产序号,这组序号最主要在追踪中其生产履历,如果纪录运用得当,它可以追踪板子上面打了哪些Date-code的电子料与来自哪个MPN,它也可以让我们追踪整个生产过程中有没有什么异常状况或是不良修理。当然这些都是有前提的,想要有什么收获就必须有付出。
电路板的生产序号印刷目前大约有4种方案,目前走在比较前面的公司会建议采用「镭雕」技术,副作用比较少,而且美观。
另外,有些跟不上脚步的公司不一定会在空版的阶段就印刷序号,而是等到分板完成后才会制作序号,序号导入在制程越前端,可以追踪到的生产履历就越完整。
2. 空板载入(Bare Board Loading)
电路板组装的第一步当然是要将空板(bare board)载入到SMT的流水线上。目前最常见的技术是将空板整齐重迭排列后,放置于料架上,然后类似印表机的纸张运送一样由机构装置从最上面的板子一片片送入SMT生产线的输送带中,不过这种运作在推送的过程中有时候会对某些板子造成表面刮伤的问题,所以有时候也会将空版放置于分料架(magazine)中,这样在机器堆送时就不会有刮伤的问题,只是多了一个放进分料架的动作。
这些过程都会有感应器(Sensor)作为眼睛传送到电脑中,然后判断何时该推送板子,并下指令何时停止板子前进。
3. 印刷锡膏(Solder paste printing)
印刷电路板(Printed Circuit Board,PCB)」进入SMT流水产线的第一个作业为「印刷锡膏(solder paste)」,说真的这有点类似女生在脸上涂抹面膜。
这个步骤会把锡膏透过钢板(stencil)印刷在PCB需要焊接零件的焊垫/焊盘(pad)上面,锡膏的位置与体积会影响到后续的焊接品质,这些锡膏会在后续SMT制程流经「回焊炉(Reflow Oven)」高温区时融化并在重新凝固的过程中将电子零件焊接在电路板上面。
之所以要使用「锡膏」来作为电子零件与PCB结合的最主要目的有二:
1)焊锡完成前将电子零件黏贴固定在电路板,使其不至于因为PCB的移动或振动而偏移。这就是为何要为膏状。
2)经过回焊高温后将电子零件焊接固定于PCB上,使其在终端用户使用的过程中不至于掉落,并达到电子讯号传递的目的。
另外,在新产品试机时有些人会使用胶膜板/胶纸板来代替锡膏,可以增加SMT调机的效率并减少浪费。
4. 锡膏检查机(solder paste inspector, SPI)
锡膏印刷的优劣会直接影响到后续零件焊接的良秀好坏,所以现在大部份较领先的EMS工厂为求品质稳定,都会先在锡膏印刷之后额外多设置一台光学仪器,用来检查锡膏印刷的品质,这台仪器就被称之为「锡膏检查机(Solder Paste Inspector, SPI)」,其原理与AOI(Auto Optical Inspection)类似,检查后如果发现有锡膏印刷不良的板子就可以先挑出来,洗掉上面的锡膏在重新印刷锡膏就可以了,或是采用修理的方式移除多馀的锡膏。
这个SPI之所以重要是因为锡膏如果经过回焊后就固化了,锡膏固化后才发现零件有焊接问题就必须动用烙铁重工,或是报废,如果可以在早期固化前就发现锡膏印刷问题并加以改善或解决,就可以大幅降低生产不良率并降低修理的成本。
5. 快速打件机 (Chip Placement, Pick and Place speed machine)
电路板上的电子零件一般分为主动元件(IC类零件)与被动元件(Inductors, Capacitors, Resistors等零件),而这类SMD被动元件(如小电阻、电容、电感)又称「Small Chip」的体积通常比较小,而且一般只有两个端点需要被焊接,所以在将这类小零件摆放在电路板上时相对的位置精度要求也比较低,所以就设计出了快速/高速打件贴片机(Chip Placement machine),这种置件机一般会有好几个吸嘴头,而且速度非常地快,快得像转轮机关枪一样,一秒钟可以打好几颗零件。
这个时候锡膏的膏状优点就显现出来了,因为打件的时候通常吸嘴头只会上下动作动,而零件的对位就得靠板子的精准移动了,这些已经被打在电路板上的电子零件则会被刚刚印刷于电路板上的锡膏黏住(这也是为何锡膏要做成膏状的原因之一),所以既使打件的速度非常的快(板子移动的速度方常快),板子上面的零件也还不至于被甩开飞散,但大型零件或是有一定重量的零件就不适宜用快速打件机来处理,一来会拖累原本打得飞快的小零件速度,二来怕零件会因为板子快速移动而偏移了原来的位置。
视电路板上的小零件数量多寡,一条SMT产线一般会有1~4台快速打件置件机。
6. 泛用型打件机 (Pick and Place general machine)
这种泛用型打件贴片机一般又称为「慢速机」。它几乎可以适用于所有SMD零件的贴片打件需求,但因为其诉求的不是速度,而是打件的精准度,所以慢速机一般拿来打一些体积比较大或是比较重或是多脚位的电子零件,如BGA积体电路、连接器(connector)、读卡机、屏蔽框/罩…等,因为这些零件需要比较准确的位置,所以其对位及角度调整的能力就变得非常重要,取件(pick)后会先用照相机照一下零件的外观,然后调整零件的位置与角度后才会置件(placement),所以整体速度上来说就相对的慢了许多。
这里的电子零件因为尺寸的关係,不一定都会有捲带包装(tape-on-reel),有的可能会是托盘(Tray)或是管状(tube)包装。但如果要让SMT机器可以吃托盘或是管状的包装料,通常需要额外配置一台机器。
一般传统的打件贴件机(pick and place machine)都是使用吸力的原理来取放电子零件,所以这些电子零件的最上面一定都要保留一块乾淨的平面给打件机的吸嘴来吸取零件之用,可是有些电子零件就是无法有平面留给这些机器,这时候就需要订制特殊吸嘴给这些异形零件,或是在零件上加贴一层平面的胶带,或是戴上有平面的帽盖。
7. 手摆零件或目视检查 (hand place component or visual inspection)或炉前AOI
当所有的零件都打上电路板在要进入高温回焊炉(reflow)前,通常还会设置一个检查点,用来挑出打件偏移或掉件…等的缺点,因为过了高温炉后如果再发现有焊接问题就必须要动烙铁(iron),这会影响到产品的品质,也会有额外的花费;另外一些无法经由打件/贴件机来操作的零件,比如较大的电子零件或是DIP/THT传统零件或是某些特殊原因,也会在这里用人工的方式手摆零件。
另外,有些手机板的SMT会在回焊炉前多设置一道「炉前AOI」,用来确认回焊前的打件贴片品质。
还有一个情况是某些板子会在SMT阶段就直接将「屏蔽罩(Shielding-can)」焊接于电路板上,一旦屏蔽罩放上电路板就无法在经由AOI或是目检方法检查其贴片与焊锡品质了,建议有这种情况一定要扩多设置一道「炉前AOI」,放置在「屏蔽罩」贴片之前。
8. 回焊 (Reflow)
回焊(reflow)的目的是将锡膏熔融并形成非金属共化物(IMC)于零件脚与电路板之间,也就是将电子零件焊接于电路板之上,其温度的上升与下降的曲线(temperature profile)往往影响到整个电路板的焊接品质,根据焊锡的特性,一般的回焊炉会设定预热区(pre-heat)、浸润区(soak)、回焊区(reflow)、冷却区(cool)来达到最佳的焊锡效果。
以目前无铅制程的SAC305锡膏,其融点大约落在217℃左右,也就是说回焊炉的温度至少要高于这个温度才能重新熔融锡膏,另外回焊炉中的最高温度最好不要超过250℃,否则会有很多零件因为没有办法承受那么高的温度而变形或融化。
基本上电路板经过回焊炉后,整个电路板的组装就算完成,如果还有手焊零件例外,剩下的就是检查及测试电路板有没有缺损或功能不良的问题而已。
9. 光学检查銲锡性 (AOI, Auto Optical Inspection) Option
虽然「炉后AOI」几乎已经成现今SMT的标准配置,但并不一定每条SMT的产线都会配置有「光学检查机(AOI)」,设置「炉后AOI」的目的之一是因为有些密度太高的电路板无法有效的进行后续的开短路电路测试(ICT),所以用AOI来取代,但由于AOI为光学判读,有其先天上的盲点,比如说零件底下的焊锡无法被检查,邻近高零件的位置会有阴影效应无法有效检查,而且目前AOI仅能针对看得到的零件检查有否墓碑(tombstone)、侧立、缺件、位移、极性方向、锡桥、空焊等,但无法判断假焊、BGA焊性、电阻值、电容值、电感值等零件品质,有些AOI连QFN或城堡形端子(Castellated terminations)的侧边焊锡都无法检查。
所以到目前为止AOI绝对无法完全取代ICT及FVT。
所以如果仅使用AOI想取代ICT,在品质上仍然会有很大的风险,但ICT也不是百分之百就是了,只能说互相弥补测试涵盖率,希望做到100%测试涵盖率,所以自己要做个取舍(trade-off)。
10. 收板 (unloading)
当板子组装完成后会在收回到分料架(magazine)内,这些分料架已经被设计成可以让SMT机台自动取放板子而不会影响到其品质,但操作时还是得注意不同板子的上下间距以避免电子零件撞件问题。
11. 成品目检 (Visual Inspection)
不论有没有设立AOI站别,一般的SMT线都还是会设立一个PCBA组装板的目视检查区,信心度还是不足啊!目的在检查电路板组装完成后有无任何的不良,如果是设置有AOI站别者则可以减少目检人员的数量,因为还是要检查一些AOI无法判读到的地方,或复检AOI判退打下来的不良。目前的技术,AOI还是有一定的误判率的。
很多的工厂都会在这一站提供目视重点检查模板(inspection template),方便目检人员检验一些重点零件的焊性与零件极性。
12. 零件后复 (Touch up)或波焊零件
如果有些零件没有办法用SMT来贴片打件,就需要后复(touch-up)的手焊零件或利用「波焊(wave soldering)」或「选焊」来焊接传统通孔零件,这个步骤通常会放在SMT的成品检查之后,目的是用以区别缺点是来自SMT还是SMT后的制程。
「后复」电子零件时要使用烙铁(iron)及锡丝(solder wire),焊接时将维持于一定高温的烙铁头接触到欲焊锡的零件脚与焊垫,直至温度升高到足以融化锡丝的温度,然后加入锡丝融化,迅速移除烙铁头以降低焊锡温度,待锡丝冷却固化后就会把零件焊接于电路板之上。
手焊零件时会有一些烟雾产生,这些烟雾会包含许多重金属,所以操作区域一定要设立烟雾排出设备,尽量不要让操作员吸入这些有害烟雾。
需要提醒的,有些零件的后复会因制程的需求而安排在更后段的制程。
深圳宏力捷推荐服务:PCB设计打样 | PCB抄板打样 | PCB打样&批量生产 | PCBA代工代料
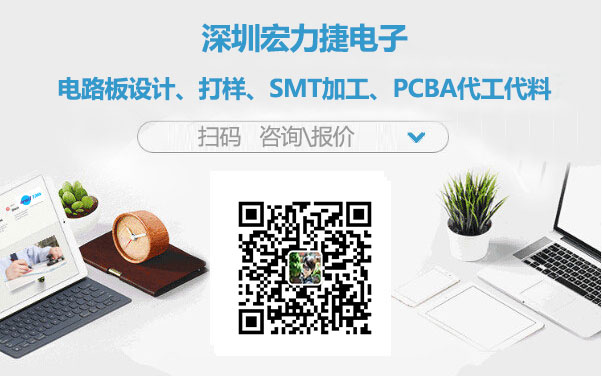